ALLIHENTROP
Informations clés
Opérateur chef de file
MATERIA NOVA (MANO)
Avenue Nicolas Copernic 3
7000 Mons
BELGIQUE
Personne de contact :
Corinne NouvellonDate de début
01-07-2018
Date de fin
31-12-2022
Eléments budgétaires
Budget Total
1 867 383,03 €
Site Web
http://www.allihentrop-interreg.eu/
ALLIHENTROP
Synthèse et mise en oeuvre de revêtements à base d'ALLIages à Haute ENTROPie

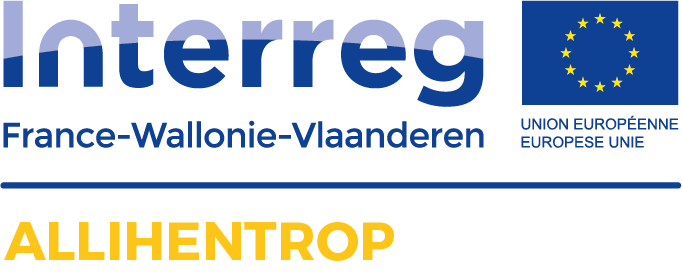
Catégorie
Projet
Objectif spécifique du programme
Accroissement de la recherche et de l'innovation de la zone transfrontalière dans les secteurs stratégiques et les secteurs à forte complémentarité
Domaine d'intervention
Activités de recherche et d’innovation dans les centres de recherche publics et les centres de compétence, y compris la mise en réseau
La filière métallurgique doit aujourd’hui être capable de répondre aux besoins stratégiques en innovation des marchés applicatifs prioritaires (automobile, mécanique, aéronautique) pour assurer sa pérennité. Il est essentiel de développer de nouveaux matériaux à hautes performances pour élargir le champ des applications vers des domaines de plus haute valeur ajoutée, tout en garantissant le respect de normes environnementales de plus en plus exigeantes. Pour répondre à ces attentes, le projet ALLIHENTROP propose de développer des revêtements hautes performances à partir d’une classe émergente de matériaux, les ALLIages à Haute ENTROPie. Il s’agit d’alliages aux compositions complexes qui contiennent un grand nombre d’éléments métalliques en proportions égales ou voisines. Ces matériaux possèdent des propriétés uniques, ils sont imaginés sous forme de revêtements dans le but d’apporter une fonctionnalité à une pièce métallique ou d’en améliorer les performances et ainsi, valoriser des matériaux supports ou structurels à faible valeur ajoutée. L’enjeu est de montrer la possibilité de faire passer ces alliages à haute entropie, de l’échelle du laboratoire de recherche à l’échelle préindustrielle.
- CRIBC
Site web : http://www.bcrc.be - Université Polytechnique Hauts de France (UPHF)
Site web : http://www.uphf.fr/LAMIH/fr/frontpage - Université de Lille
Site web : http://umet.univ-lille1.fr/
- EURAMATERIALS
Site web : https://euramaterials.eu/ - MECATECH
Site web : https://www.polemecatech.be - I-Trans
Site web : http://i-trans.org
Date de rapport 30-05-2023
L'objectif du projet est de développer des revêtements haute performance à partir d'une classe émergente de matériaux, les alliages à haute entropie (HEA). Ces alliages sont constitués d'un grand nombre d'éléments métalliques ce qui leur confère des propriétés uniques en termes de dureté, résistance à l'usure et à la corrosion. Dans le cadre de ce projet, des alliages quinaires sont appliqués sous forme de revêtements afin d'apporter une fonctionnalité nouvelle ou améliorée aux pièces traitées. L'apport de la modélisation par ULille a permis de définir un premier alliage quinaire (5 éléments métalliques). La stabilité de la phase Cr23C6, présente dans l'alliage sous forme massive, et des différentes phases présentes lors du refroidissement a été étudiée. Des poudres d'alliages mécano-synthétisées à ULille-UMET et des mélanges de poudres commerciales sont utilisées pour la réalisation de cibles et l'application de revêtements minces par pulvérisation plasma à Materia Nova, ou de revêtements épais par procédé laser au CRIBC. Les dépôts de couches minces sont réalisés sur acier ainsi que sur des substrats spécifiques tels que des acier polis pour faciliter les caractérisations mécaniques et tribologiques (au LAMIH-UPHF) ou silicium et pastilles KBr pour les caractérisations physico chimiques. Les duretés sont assez proches de celles généralement obtenues par chromage électrolytique électrolytique ce qui constitue un résultat très positif de ce projet et encourage la poursuite de développement. Une dureté plus élevée ainsi qu'une meilleure résistance à l'usure ont été observées pour les dépôts issus de poudres d'alliages mécano synthétisées. La présence de carbone dans les poudres mécano synthétisées et donc la formation de carbures semble être responsable de ces différences de propriétés. La composition chimique des revêtements (EDX) est homogène et similaire à celle des cibles et mélanges de poudres initiaux. Les dépôts sont stables en température, sans évolution de la structure cristallographique (DRX-MET) jusque 800 ou 950°C ni du caractère paramagnétique (spectroscopie Mössbauer). Ils sont composés de nano-domaines. Par la suite, il a été observé qu'un apport d'énergie au film en croissance engendrait une modification de sa stœchiométrie (composition chimique). La composition des films est donc modulable par ajustement des paramètres de dépôt, à partir d'une même cible. Cette évolution de composition s'accompagne d'une densification de la couche et d'une augmentation de sa cristallinité, qui engendre, d'un point mécanique et tribologique, une augmentation de la dureté et une meilleure résistance à l'usure. Finalement, cette évolution des propriétés fonctionnelles serait liée à la densification et la cristallisation du film plutôt qu'à sa composition chimique. Les couches épaisses (> 10 µm) sont réalisées par technique laser, sur des aciers à bas taux de carbone. Le principe consiste à déposer une encre contenant un mélange de poudres métalliques commerciales (de composition identique à celles des couches minces), d'un solvant et d'additifs organiques. Ce dépôt est ensuite traité par laser avec un traitement impliquant la fusion globale des différents métaux. L'optimisation de la composition de l'encre et des paramètres laser a permis l'obtention de revêtements de structure parfaitement cubique centrée, d'épaisseur comprise entre 30 et 80 µm, en fonction de l'épaisseur initialement déposée. Par rapport à la composition initiale, le revêtement présente une sur-stœchiométrie en fer attribuée à l'apport du substrat lors du traitement laser. L'observation de la tranche des revêtements par MEB montre une microstructure homogène, formée de grains de quelques microns. Une bonne adhésion du revêtement sur le substrat est observée. D'autres dépôts ont également été préparés à partir de mélanges quaternaires, le cinquième élément, à savoir, le fer, étant apporté par le substrat. Des résultats plus que satisfaisants sont obtenus pour la composition CoCrFeNiMo, qui permet d'obtenir un revêtement homogène, dense et d'épaisseur de l'ordre de 100 microns, par une approche de dépôts multi-couches. En parallèle, une autre voie de développement de revêtements épais a été initiée, via la technologie SPS. Celle-ci, outre l'obtention de revêtements d'épaisseur plus importante, permet de pallier certains écueils de la technologie laser et notamment l'oxydation de certains éléments métalliques, tels que l'aluminium. Des revêtements de composition Al19Cr22Fe34Mn19Mo6 d'épaisseur de l'ordre de 300µm ont ainsi été obtenus, revêtements dont la dureté est identique à celle mesurée sur des dépôts couches minces de même composition. Finalement, de nouveaux revêtements de la famille quinaire initiale (AlCrFeMnMo) ont été déposés sur un substrat noble, lncoloy 945, superalliage, à base principalement de nickel, de chrome et de fer, présentant une haute résistance à la corrosion mais une faible dureté. Des revêtements quinaires épais (environ 120µm), composés, de manière relativement homogène, des mêmes éléments que l'alliage de base et enrichi en nickel provenant du substrat ont été obtenus sur ce substrat. Une dureté largement supérieure à celle du substrat nue a pu être obtenue après revêtement. Par ailleurs, tout au long du projet, la thématique et la potentialité des HEA ainsi que les résultats du projet ont été présentés, dès que possible, lors de conférences, webinar ou salons. Des articles scientifiques, disponibles sur le site internet du projet (www.allihentrop-interreg.eu) ont été publiés. Le public visé est donc à la fois scientifique et industriel. Presqu'une centaine d'entreprises, situées tant sur les deux versants concernés par le projet qu'hors zone (en France hors zone ou en Europe) ont ainsi été sensibilisées.